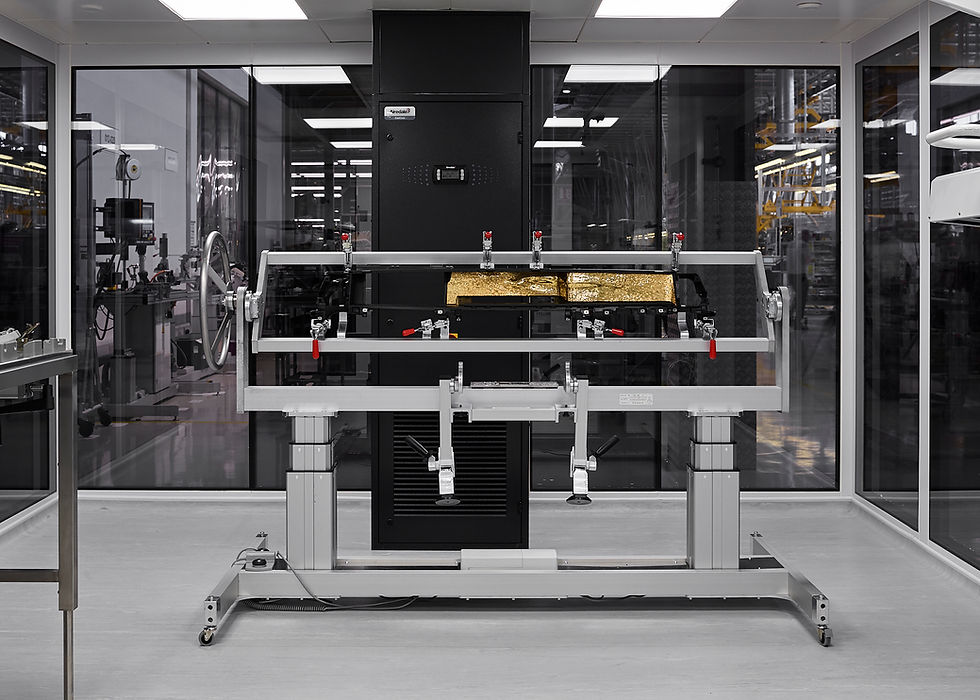
Rolls-Royce Motor Cars has commissioned a highly technical Clean Room at its manufacturing facility at Goodwood, West Sussex. Similar facilities exist in microchip manufacturing plants and in pharmaceutical and medical equipment production facilities.
The primary purpose of the Clean Room is to provide a sterile environment within which delicate and highly bespoke items can be assembled.
The eighth generation of Rolls-Royce Phantom brings with it an unprecedented opportunity to exhibit works of art and design within the motor car itself, in an area named, the Gallery. The Gallery is formed of an uninterrupted piece of glass which spans the width of Phantom’s fascia, behind which a recess presents an illuminated stage, an area for patrons to embrace the unique storytelling characteristic of the marque.
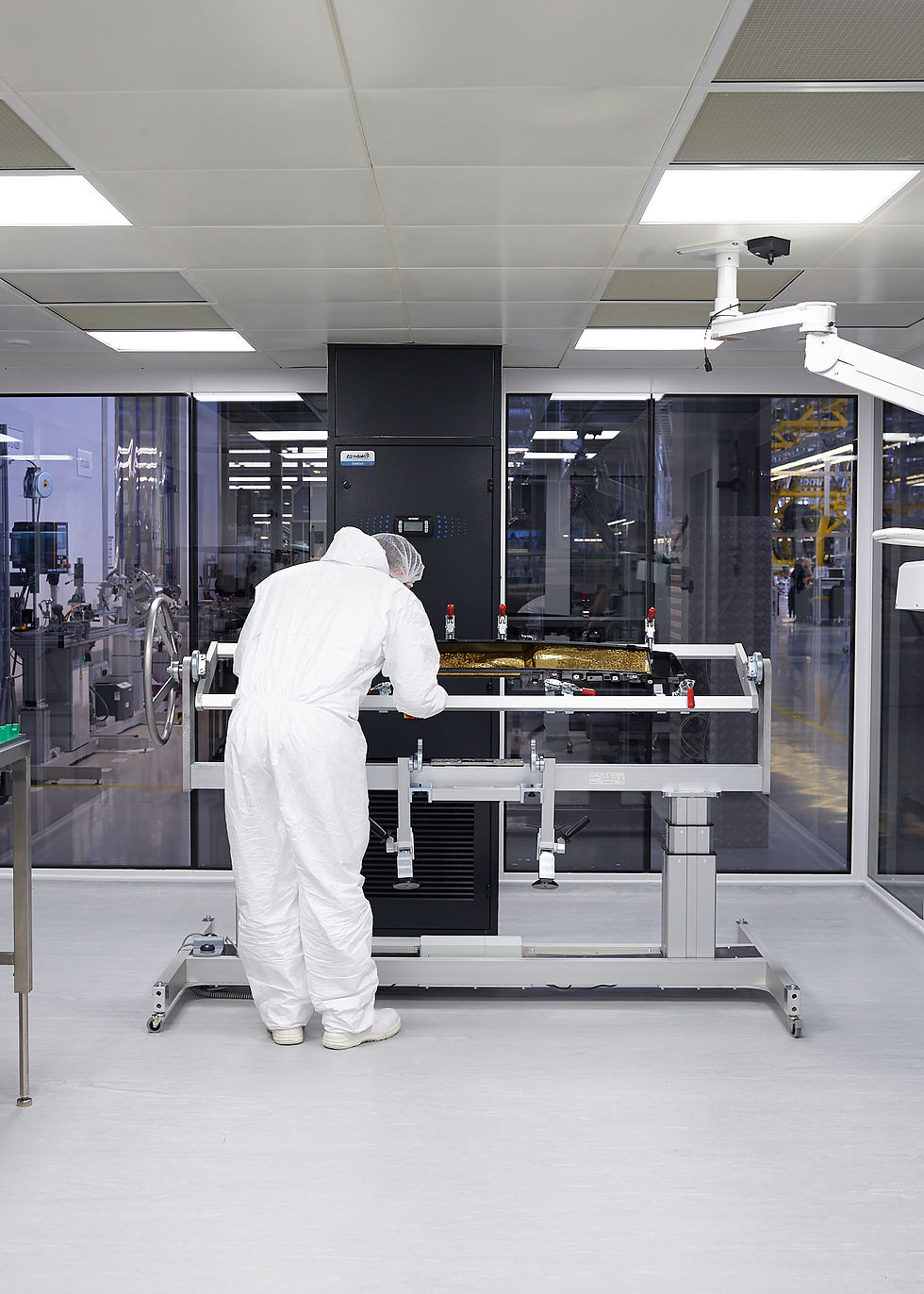
At the conception of the Gallery, a requirement for clean manufacturing was identified and extensive research was conducted in order to create a Bespoke Rolls-Royce Clean Room at the marque’s headquarters in Goodwood, West Sussex – itself a Global Centre of Luxury Manufacturing Excellence. The lifespan of Phantom is remarkable, with over two-thirds of all Rolls-Royces created over the marque’s 116-year history still in road-worthy condition. It is therefore essential that the Gallery can stand the test of time by preserving precious and personal items for as long as the motor car itself.
Experts from the Home of Rolls-Royce visited pharmaceutical and microprocessor Clean Rooms to fully understand these complex manufacturing laboratories and learn of the procedures and requirements necessary to create a medical grade, particle free, sterile enclosure. Even a minute speck of dust would detract from the aesthetic perfection of the Gallery. The assembly therefore requires meticulous attention to detail.
The Gallery Clean Room contains four medical grade, positively pressurised spaces. A highly technical sensor continually measures the particulate concentration of each space. Any particulates measuring above 0.001 of a micron are detected, a staggering statistic considering a human hair is between 50-100 microns in diameter. This process enables continual assessment and the opportunity to identify areas for improvement. If contamination is detected, the Gallery Clean Room associates are able to identify exactly when and where the contamination took place, in order to improve future assembly. Planning and quality engineers monitor daily the particle count inside the Gallery Clean Room to ensure that no deep cleans that might interrupt daily production are required.
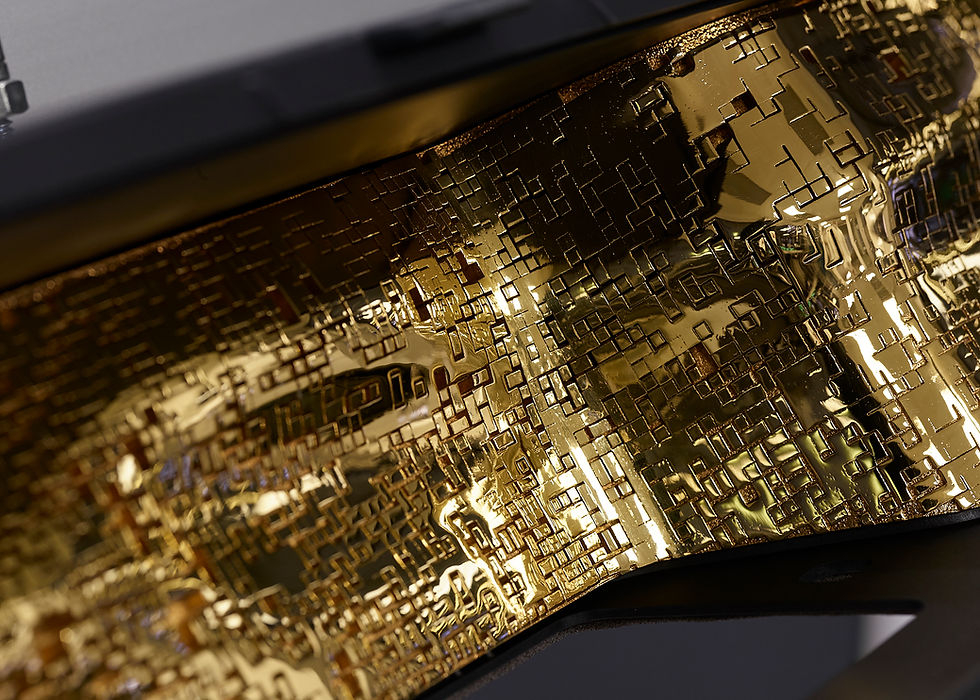
A complex filtration system is built into the ceiling of the Gallery Clean Room to continually remove unwanted particles from the re-circulating air. This system is, for aesthetic reasons, covered in a wooden veneer – this is, after all, situated at the Home of Rolls-Royce.
There are only five associates at the Home of Rolls-Royce trained to operate in the Gallery Clean Room, with only two permitted to enter at any one time. These associates must comply with strict guidelines to prevent possible contamination. No cosmetics, hair products or deodorant may be used.

The first enclosure is charged with sanitisation. It is here that associates prepare to enter the body of the Gallery Clean Room by dressing, top-down, to reduce the risk of hair and other imperfections soiling clothing. Medical-grade, lint free surgical clothing must be worn at all times, including a hairnet, a sterile mask, surgical overalls and overshoes. Associates must have previously cleaned their hands using deionised water, preventing possible contamination from soap and regular water. Bespoke non-powdered latex gloves have been developed specifically for Rolls-Royce to ensure moisture generated due to perspiration in this highly pressured environment is contained 100% within the glove.
Alongside the Gallery Clean Room is the Logistics Enclosure, where art and engineering first meet. The artwork enters the chamber wrapped in a protective film, inside two hermetically sealed containers. The outer package is discarded, the inner package is cleaned in preparation for entering the next laboratory. Componentry enters here in an identical format.

The Preparation Room is the next stage of this intricate journey. Entry is via an airlock, with each room becoming further pressurised to create a compression chamber. The increasing atmospheric pressure ensures that air only flows out of the facility. The artwork is delicately removed from its packaging and cleaned on a specially created machine, or ‘extract bench’. Here, any dust particles are extracted whilst the associate uses ultra-violet light and a powerful magnifying glass to identify any imperfections. No foreign objects are allowed to enter this space, even paper is forbidden.
The final enclosure is the Operation Centre, in which the micro-assembly takes place. This space is as atmospherically pure as humanly possible, with only one Phantom Gallery, and one Rolls-Royce Associate, permitted entry at a time. This room is deep cleaned each week in a process that takes up to eight hours. Any componentry entering the space must also have been through an intensive cleaning process. All metal elements, no matter how small, must be sanitised in an ultrasonic cleaner at 70 degrees for a period of 52 minutes. Further ultra-violet light examinations take place before the final assembly and the artwork is finally sealed within Phantom’s Gallery.
Comentarios